1970 Dodge Challenger R/T SE
440 Magnum 3 speed Torqueflite 3:23's
Owner: Barnabas Kriss
Location: British Columbia
December 2006's Mopar of the Month is the incredible restoration done by Barnabas Kriss of this 1970 Challenger R/T SE. I will let Barnabas tell the story of the car and its restoration:
We purchased this car in August 1993 as a restoration project. We found this car in the spring of 1993 while looking for parts for our previous car, a 1970 Cuda. Not much is known about the history of the car. It was sold new by Luckey Dodge in Longview, Texas. The previous owner bought the car in 1989 and brought it to Canada. At this point the car was already in non-running condition. During the restoration we discovered evidence that the car probably had a very rough life. While the car was a partially disassembled basket case, it was one of 733 R/T SE Challengers built with 440/automatic. It also had its numbers matching drivetrain, many factory options, and minimal rust.
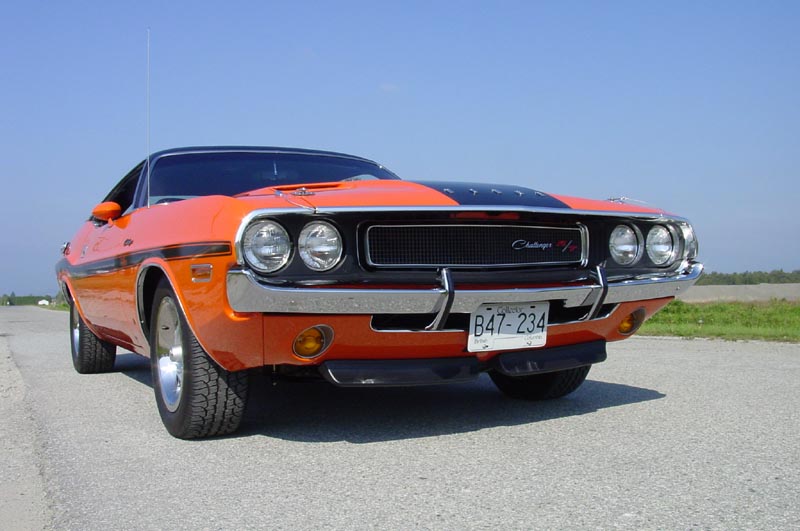
Before starting the restoration, all details were documented and researched. We decided to make a few minor deviations from stock, because of personal preference. We also started collecting NOS and nice used parts. Many smaller items were still available from Chrysler such as emblems, door handles, a few moldings, front valance panel, battery cables, etc. Special thanks goes to Coquitlam Chrysler parts department for their help. Many more NOS parts were collected form about 30 different states and at least five Canadian provinces
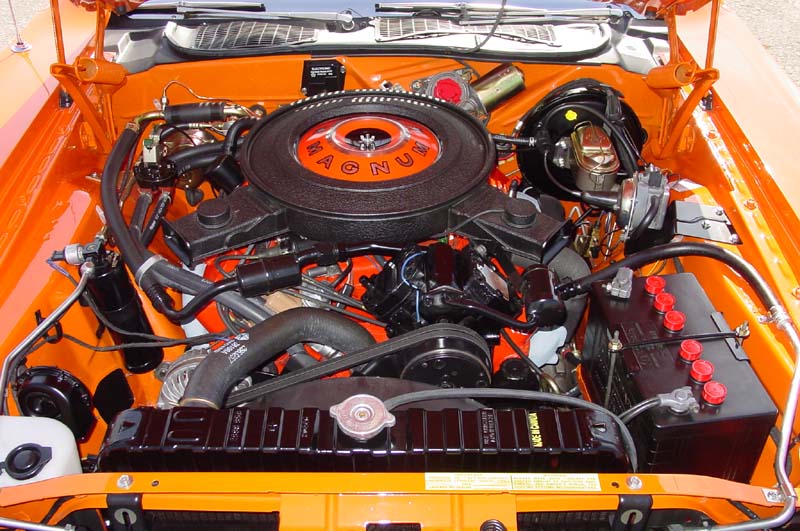
Once a significant part of the hard to find parts were in hand, The car was completely disassembled to a bare shell. Minimal rust repair was needed, only the trunk floor and the driver's side inner fender had to be replaced. Minor rust repair was also needed on the driver's side floor pan, on the seams between the roof and the quarters, and by the lower corners of the windshield. The factory spot welds were carefully duplicated for a correct look. In areas where patch type repairs were necessary, the metal was butt-welded edge to edge with no overlap. The welds were ground smooth on both sides, making the repair invisible. Dents were removed as much as possible by hammering, and shrinking the metal as necessary. This process is extremely time consuming, but the need for much body filler is eliminated. The paint preparation took well over 300 hours.
The body, and all sheetmetal parts were then taken to Redi-Strip for a chemical dip. This involves a caustic bath to remove all paint and dirt, followed by electrolytic derusting, and finally a zinc phosphate coating for corrosion resistance. The body was then mounted on a rotisserie, and epoxy primered inside and out. The inside of the framerails and other difficult to access areas were also rustproofed. Primer was poured into areas like the trunk floor extensions until it began seep out of the factory seams. New seam sealer was applied as specified in the factory service manual.
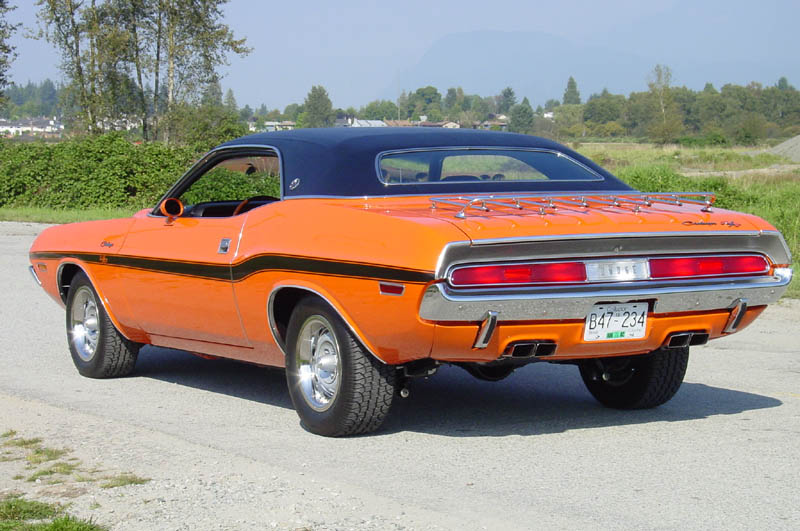
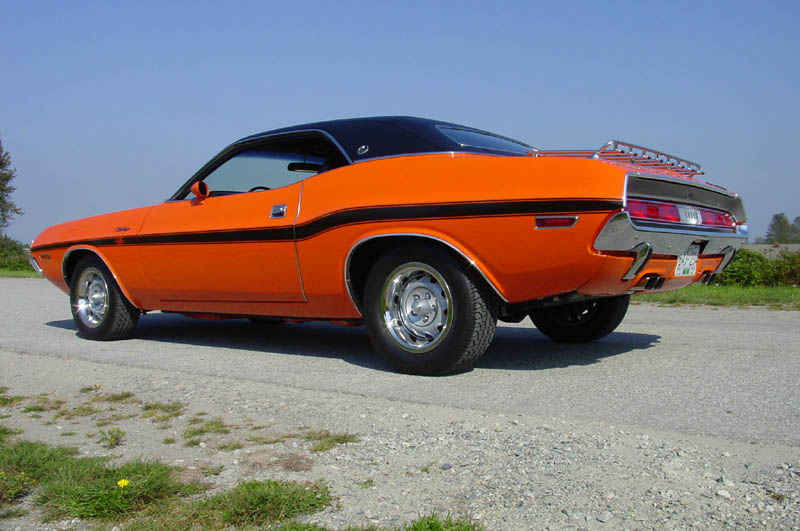
Next the hood hinges and door hinges were rebuilt to better than new condition. The door hinges are a poor factory design, so we improved on the design while maintaining a correct appearance. Body panels were then installed and aligned. The body was then sprayed with a sealer and blocksanded. The engine compartment, undercarriage, etc were also blocksanded and prepared for paint. RM Diamont basecoat-clearcoat paint was used. Finally the body was wetsanded and polished. The exterior painting, wetsanding and polishing was done by A & S Autobody in Maple Ridge, BC.
All parts were correctly refinished before assembly. Small parts were zinc or cadmium plated as they were originally, nuts and bolts were phosphate coated, etc. All suspension parts and engine accessories were powder coated in original colors for a correct appearance. The exhaust manifolds were metallic-ceramic coated to prevent surface rust. All stainless steel moldings were polished, and all plated parts were re-chromed by Modern Auto Plating in Vancouver, BC.

Assembly was started with the installation of the new reproduction vinyl roof. The assembly process was done in almost the same sequence as at the factory. All parts were rebuilt to look and function like new using original Chrysler parts where possible. Every part was rebuilt: windshield wiper motor, AC/heater box, AC compressor, alternator, PS pump, steering box, steering column, etc. The original carburetor was sent to the Holley Custom Shop for restoration. Most of the parts but also have the correct date codes: alternator, voltage regulator, coil, spark plug wires, carburetor, intake and exhaust manifolds, etc
.
The rearend and transmission were also completely rebuilt and detailed. All original inspection marks were re-applied. New reproduction gas tank, fuel, and brake lines were installed.
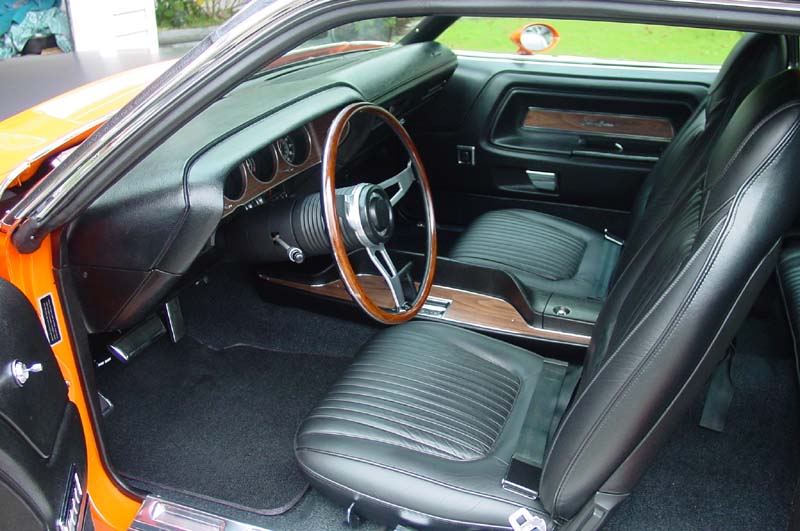
The engine block and all parts were taken to Redi-Strip for cleaning and derusting. All internal parts were replaced except the crank and rods. Machining was done by Thunderbolt Engines in Langley, BC. The heads received mild porting and were upgraded with hardened valve seats and stainless steel valves for unleaded use. The compression ratio was blueprinted to 9.5:1. The rotating assembly was balanced, and all dimensions were blueprinted to factory specifications. Engine assembly was done by myself.
The engine and transmission were installed from the bottom up like at the factory. A Chrysler electronic ignition system was installed hidden from view. The correct part number radiator was recored. A reproduction exhaust system was installed. The suspension was completely rebuilt with all new parts. The brakes were rebuilt with OEM Chrysler parts. The stock 11" front rotors were upgraded to the 11.75" rotors. New 15x 7 rallye wheels with NOS centercaps and new BFGoodrich Comp TA tires were installed.
The last area to be finished was the interior. The headliner and overhead console were recovered with the correct fabric. Locating the correct fabric required some research, as most of the reproduction parts vendors and upholstery shops only carry incorrect replacements. The carpet was replaced with a reproduction. The console was replaced with a good used piece. The original doorpanels were cleaned and detailed. The seats needed to be completely restored. The seat adjusters were completely rebuilt. The old seat foam and upholstery were removed and the seat frames were repainted. New molded foam and reproduction upholstery was installed.
The last item to be restored was the grille. The grille was disassembled, the old anodizing was stripped, the aluminum was polished and re-anodized using the OEM bright dip process. All parts were repainted and the grille was assembled using the correct rivets. Finally the grille was installed along with the NOS headlight bezels.
There were a few NOS items which were extremely difficult to find. One was the front valance molding which was installed on SE models only, the other was the door edge guards, which are an unusual option on a Challenger. We were searching for these items for about three years. The dashpad was another hard to find item, specific to 1970 models with AC.
The project was finished in July 1999, after investing many thousands of dollars, and about 1600 hours of work. The restoration was completed by myself (Barnabas Kriss) and my father (Gabor Kriss).
We have entered the Challenger in several shows since. The car has received about 20 first place trophies, as well as awards for best engine, outstanding paint, outstanding musclecar, best restored vehicle, and best of show.
Mopar of the Month
November 2014
Mopar of the Month
December 2006
Mopar of the Month
November 2014
Mopar of the Month
December 2006